The meeting of worlds
You have worked hard, built up your business, and are now in a place where you can make a capital investment that will see you stop buying in print. You may be a wide-format virgin and looking to invest in your first machine to bring some production in-house, or perhaps already own a dedicated device and are looking for a second to handle all your requirements.
Whatever your situation, one thing will be certain, it is no easy task. You may know exactly what your business needs right now to service its most popular product ranges, but the likelihood is that the shifting tides of consumer demand will change this reality in the future.
Another factor is that not only do you have to choose from a myriad of ink technologies from basic solvent through to exotic latex technologies, but you have to decide what kind of printing you want to do.
Is it going to be all onto vinyl and paper-based substrates, using laminators to apply print to rigid substrates as required? Or do you still need to cater for a growing demand from customers that require high quality quick turnarounds—and thus direct-to-substrate printing on rigid materials such as plastics, wood, foam-board and metal? Well, if the choice is just too difficult to make, then why not at least narrow down your list and go for a hybrid machine that offers the ability to flex between roll-to-roll and flatbed printing?
The challenge
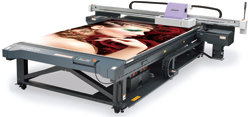
The hybrid Mimaki provides an advantage to those
sign-makers and print-service-providers whose
output requirements flex between roll-to-roll and
flatbed printing in higher volumes
Choosing a wide-format device with hybrid capability is a much-debated topic, with supporters and detractors on both sides. A range of experts argue that the technology always leans towards one strength, so either roll-to-roll or flatbed, with the other remaining too weak to base a business on—a challenge that a number of manufacturers are now overcoming. However, the other side of the argument is that your business will always lean towards doing a majority of printing in one format or the other. As such, you should go for a hybrid device with that strength and use its flexible capability to branch out and start saying yes to more work—buying a dedicated device when demand is at a level that it will make a good return on investment.
“The ability to print onto rigid substrates and also roll-fed material is something that a lot of print service providers are increasingly requiring, not only to save precious floor space but also to offer consistency of print finish. Machines capable of producing both types of output offer advantage both in reduced capital investment and ongoing flexibility within their print capacity,” argues Mike Lewis, industrial products sales manager for Mimaki’s exclusive UK and Ireland distributor, Hybrid Services.
Mimaki’s offering in this arena focuses down on its UJV-160, described as a ‘true hybrid’, in addition to the more industrial JFX500-2131, soon to be launched on the UK market. This reference to true hybrid highlights another fierce debate going on in the hallowed halls of manufacturer marketing departments across the land.
The variety of ink configurations that Mimaki offers across its UV range is a huge strength”
A true hybrid machine is one that can move between roll-to-roll and flatbed without having to do any lengthy changeover of tables, attachments and calibration. This terminology also applies to those machines that can print both roll-to-roll and flatbed with equal strength, as mentioned previously this overcomes the oft sighted criticism of hybrid technology—that it is a jack of all trades and master of none.
Still classed as hybrid though is those machines that need to be fully set up and calibrated for flatbed or roll-to-roll, but take some fairly extensive work to do so. A hyrbid is also those devices, such as the JFX500-2131, that concentrate it strength in one area with an ancillary alternative. In the JFX’ case , it has all the capabilities of a dedicated flatbed, but has an integrated roll-to-roll option that, while unable to cope with industrial requirements, is ideal for most of the demands of your average project.
Lewis continues: “The variety of ink configurations that Mimaki offers across its UV range is a huge strength. As Mimaki’s exclusive distributor, we know from experience that when surface printing with UV ink; wash trials, scratch and chemical resistance results will vary dramatically depending on the substrate and application, so finding a versatile, complete solution to accommodate all the end users’ applications is something we are confident we can achieve. LED UV curing enables an easy print process to even heat sensitive media so a broad range of roll fed substrates can be printed on the same machine that’s capable of outputting to 10mm thick board.”
The central question for most sign-makers though is; if I go for a hybrid option, then what opportunities will it open up that a dedicated device can’t? Drawing on his extensive customer facing experience, Lewis suggests an answer: “The Mimaki UJV-160 is a perfect stepping stone into direct to substrate UV printing. It offers an affordable solution, easy operation, minimal floor space is required and it is very quick to change between roll and rigid substrates.
“This has been an extremely popular solution for printing wallpaper, creative window graphics and also for anyone printing packaging and lighter boards for retail point-of-sale/exhibition graphics/creative props. With a 1.6m print width and featuring a powered take-up unit, it’s standard sized for the sign industry, but the inclusion of foldaway tables enables 10mm thick board to be printed to, with a weight of up to 12kg; opening up many new product lines. The new Mimaki JFX500-2131 that hits these shores in quarter four will offer full production speeds of 60sq m/hr and is anticipated to have true roll-to-roll capabilities as well.”
Versatile values
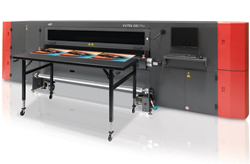
The EFI Vutek QS2 Pro features UV grayscale print
technology is designed for sign-makers that need a
machine with a balance of flatbed and roll-to-roll
printing strengths
The UK often sits just behind the curve in the adoption of major developments in sign and display technology, this is normally down to the fact that suppliers and manufacturers have tended historically to use continental Europe and the USA as launch sites. This trend has changed to some degree, with power-house economic areas such as Brazil and Asia now seeing more of a focus for new launches.
The advantage for the UK sign and display industry is that its members can see how new business models pan out, before market forces kick into action and the technology becomes more established. A key trend to take note of therefore from European neighbours, and to some extent our American cousins, is that being able to be versatile when it comes to manufacturing products and services is a must—driven by consumers who have more choice on offer than ever before when it comes to fulfilling their sign and display needs.
Speaking to Marc Verbeist, international public relations manager at wide-format print technology developer EFI, he explains how demand for hybrid printer technology is evolving across its pan-European consumer base and highlights what is driving it.
“Today’s users of wide-format printing machines increasingly need the versatility from a single platform, which is designed to work efficiently with rigid and flexible materials. As well as the obvious advantage when making a single investment instead of having to buy two independent systems, there is also the consideration of reducing overall footprint with a combination unit, consolidated operator understanding who only needs to understand one engine and, of course, the simplification of file handling, RIPping and workflow.”
Today’s users of wide-format printing machines increasingly need the versatility from a single platform, which is designed to work efficiently with rigid and flexible materials”
Verbeist continues: “Any company wanting to increase its throughput using a wide-format UV-curable system will benefit from EFI’s design and construction parameters incorporated into its true combination wide-format and VUTEk solutions.
“These take into the account the specific, separate requirements when printing to rolls and to flat sheets, such as feed and material handling, fast changeover from flat-bed to roll-fed and back again, head height adjustment on a range of thicknesses and efficiency of operation in both modes.
“The versatility of EFI’s hybrid printers means that they appeal to first-time investors and those entering inkjet production from the offset and screen-printing sectors, as well as to experienced print-service-providers, who want to optimise their production on a true hybrid platform, so that all rigid and flexible materials can be used without compromise.”
If you build it...
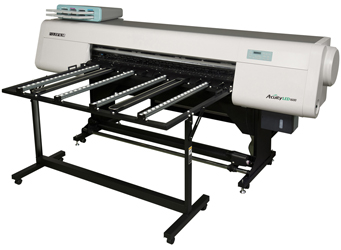
The Fujifilm Acuity LED1600 has been designed to allow firms
which carry out a majority of roll-to-roll printing work to diversify
into flatbed printing and build up its products and services in
this area
Another major print technology developer that has diversified into the hybrid wide-format printer market is Fujifilm. The multinational made the move into wide-format earlier than many of its peers, a decision that, in hindsight, they must be very happy with considering the position of its global competitors such as Kodak—which never made the leap.
Fujifilm’s two flagship hybrid options take the form of the Acuity LED 1600 and the Acuity Advance. Both systems are purposefully designed to have a key strength, with their respective alternative capabilities aimed at providing for low-volume runs. The LED 1600 has a roll-to-roll unit with the ability to attach flatbed tables, while the Advance has full-production flatbed capability, with the ability to witch to an integrated roll-to-roll unit.
“Depending on the customer’s likely production needs, they can either bias towards roll-to-roll or flatbed when considering where to place their investment,” explains Fujifilm’s product manager for inkjet, Steve Cookman.
He continues: “Fundamentally, hybrid devices are products that can handle a wide cross section of work. I think the customer has to decide for themselves whether the majority of the work they will be taking on is roll-to-roll or rigid. If the majority of your work is going to be rigid, then it doesn’t make sense to go for the Acuity LED 1600. In this instance the Acuity Advance would allow you to cater for your demand, but give you the option of taking on roll-to-roll work when required, rather than turn it away.”
The cost of the Advance is double that of the LED 1600 however, a reflection of the relative return-on-investment that can be made with the two technologies and the complexity of printing direct-to-substrate rapidly, in high volumes, at a top quality resolution. Cookman advises that the time it takes to change between disciplines on both devices is a matter of minutes.
“The entry point for the roll-to-roll device is significantly less expensive than the flatbed. We see the roll-to-roll device going into businesses that may already have some lower end solvent devices,” says Cookman, adding: “The Acuity LED 1600 is a device with a lot of industrial gauge engineering going on inside of it. Unlike some lightweight shells out there, it has a heavy duty carriage for the print heads to traverse. Its inkjet heads are from the same family as the Inca Onset, and bearing that in mind I would say it is a device that can be driven quite hard. The key point is that its productivity and durability mean it is easier to achieve a much better return-on-investment.
Although it has the appearance of a low-volume entry-level unit, put it in production and give it a run for its money, and it will pay dividends”
“Although it has the appearance of a low-volume entry-level unit, put it in production and give it a run for its money, and it will pay dividends. If you look at the demographic, I don’t see it going into the really small shops, I see it going into companies that know how to produce value added print and have sales staff that are going out actively promoting their print capabilities.
“We find some customers want an additional machine that is flexible because they get a mix of work and they don’t want to interrupt their high-end production systems.”
Pressing Cookman on why a sign-maker or print-service-provider should invest in hybrid technology, I suggest that its key strength is that it provides the first stepping stone to a diversified business. So, if you do mainly roll-to-roll work, then a hybrid device set up for this strength can fulfil your core needs, but if you get a customer ask for short-runs of rigid work, you can say ‘yes’, rather than turn the work away. This in turn allows you to build up a solid customer base over time for rigid work, which could lead to investment into a dedicated flatbed device down the line. Importantly, the hybrid then still loses none of its use, as it can still be used as a ‘mop up’ device when production volumes go very high.
“I can accept, understand and agree with that,” says Cookman, adding: “This is where the LED and the Advance are situated and give you the capabilities to choose your development path. The most important thing is to avoid the disappointment of having to invite a customer to go to competitors because you can’t do something for them.”
Fujifilm has made a number of company acquisitions in recent years to pursue its inkjet diversification strategy, leading to a $2bn investment last year into research and development, a 5 percent increase on 2011’s figures. With this in mind, Cookman adds: “If you look at that level of expertise in house, then the message to our customers is we are investing heavily in our inkjet capabilites and will continue to move forward. Perhaps not as quick as some would like, but we tend to take several steps forward at one time, rather than jumping on ever bandwagon.
“You hit the nail on the head when you said that people would tend to invest in two dedicated devices if they could. There is an argument for this at the moment, as hybrid devices tend to be too weak for full production on both formats of output. This is not to say we won’t get there in terms of devices that are equally strong roll-to-roll and rigid as a matter of course, it will just take some time.”
A hybrid future?
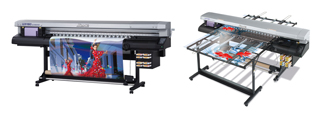
The Mimaki UJV-160 is described by exclusive UK and Ireland
distributor, Hybrid Services, as a ‘true hybrid’, and a ‘stepping
stone’ into direct-to-substrate UV printing
When I first became editor of
SignLink in August 2010, hybrid print technology was billed as the new hot kid on the block, with aspirations for wide-format printers to morph into machines that could apply ink to anything from pens to piano lids. But the hype around it has somewhat levelled of, with manufacturers going back to the drawing board to develop solutions that address key areas of demand. So what lies in store for hybrid print technology?
“A combination of speed, quality and versatility will dramatically change in the coming years. Productivity gains coupled to Mimaki’s usual focus on ultimate output quality can be seen in the very next generation machines—the JFX500 is set to deliver speeds that exceed current solutions by two and a half times, yet delivering even higher print quality,” claims Hybrid Services’ Lewis, who adds: “Sign and graphics companies will also be able to offer a broader ranges of products, with shorter lead times, that are geared to bespoke, direct-to-substrate output.”
EFI’s Verbeist also weighed in on the issue: “We expect an intensification of current trends. EFI’s wide-format printers and VUTEk platforms already include all the essential elements, which users expect to benefit from in a true hybrid solution. These machines are developed to provide true combination printing capabilities, without compromise. Essentially, fast change-over and sophisticated flat-bed and roll-to-roll media handling lead to error-free production.”
Verbeist continues: “The key to hybrid printer technology is the combination of flexibility across all material types, the best levels of quality on rigid and flexible media, and fast throughput speeds.
“Another factor is that productivity can be optimised on a true combination printer, with time-saving features and fast set-up times in a single machine. This ensures a faster and more realistic return-on-investment and total-cost-of-ownership then were a company to purchase separate flat-bed and roll-fed solutions.
Another factor is that productivity can be optimised on a true combination printer, with time-saving features and fast set-up times in a single machine”
“EFI’s VUTEk GS3250LX has also led the way with our ‘cool cure’ LED curing lamps, broadening the range of flexible materials that can now be printed on a quality combination machine. This 3.2m solution achieves high speed, faultless production on rigid substrates, including continuous boards, yet also is ideal with heat sensitive films thanks to the low temperature curing. So, the technology’s future can only be a bright one.”
When applied to technology, hybrid is a word that always conjures up, for me at least, an air of mystery and excitement. It hints at something which brings together the best of two worlds to create something that is versatile and perfectly suited to its purpose. A hybrid car uses far less fuel than conventional petrol and diesel driven machines, yet it has none of the restrictions of electric cars. A hybrid bicycle likewise allows you to spin through the city at respectable speed, yet it can handle conditions that would see a race bike cease to become ridable. Yes, you may give up the ultimate strengths of using dedicated technology, but in today’s rapidly changing world, being flexible might be the shortest route to success.
hhhh